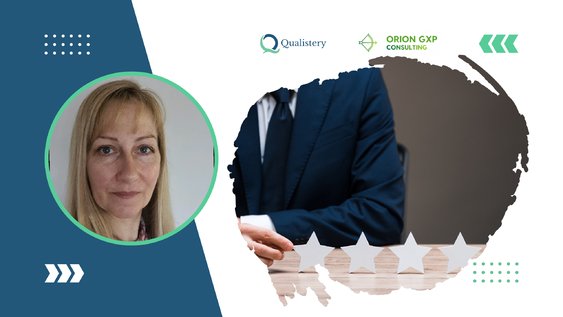
Unlocking the Power of Root Cause Analysis in Quality Management Systems
Kay Flahive
Course Overview
The Good Manufacturing and Good Distribution Practice guidelines expect all departures from the guidelines and a company’s documented QMS to be documented via an investigation. So, what is the difference between an investigation and a good investigation, and what relevance does the Root cause analysis have to an investigation?
An effective RCA process will list all potential causes connected to the deviation/ non-conformance that has occurred. RCA can use several different tools, and some methods may suit the issue at hand better than others. The company’s RCA SOP will guide/ highlight some of the key RCA tools available to understand the root cause of the deviation/ non-conformance.
In this webinar, we will examine what constitutes a good investigation and why it matters so much that we get this right. We will also briefly examine some examples of good and bad RCAs and introduce the appropriate tools and techniques that we would employ depending on the situation/ deviation/non-conformance. Unfortunately, no one-size-fits-all tool exists, and each method has its pros and cons.
All of the above can only be achieved with the correct engagement from the key stakeholders within a company. A good investigation and effective root cause analysis cannot be achieved solely by an individual within a company. This needs to be a collaborative effort, and we will see why this is so important during this webinar.
What You'll Learn?
- Understand what is Root Cause Analysis and why is it important
- Learn The Background of Good investigation practices
- Access a range of tools, CAPA and linking to Root Cause
- Quality assurance employees
- Quality managers
- Regulatory managers
- Quality directors